In modern manufacturing, the allure of unattended, “lights-out” machining is undeniable. The prospect of machines tirelessly churning out precision components with minimal human intervention is attractive for job shop owners, increased efficiency, cost-effectiveness, and labor dependency.
One manufacturing process that has benefited from this automation revolution is electrical discharge machining (EDM)–specifically, wire-cut EDM machining. This article explores how automated and unattended wire EDM solutions help machine shops meet the demands of a rapidly evolving manufacturing landscape.
What are the Benefits of Unattended Wire EDM Machining for Machine Shops?
Automating EDM production can extend a lifeline to job shops and precision manufacturers, offering benefits beyond conventional CNC equipment automation.
While the universal benefits of reduced labor costs, enhanced productivity, and improved consistency still apply, automating wire EDM machinery brings additional value:
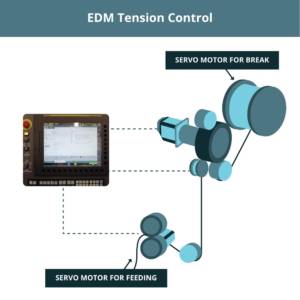
Automated and advanced EDM systems detect wire feeding and tension problems. These features support longer, unattended jobs.
- Minimized labor costs. Unattended wire EDM reduces human supervision. By running machines around the clock, job shops can significantly reduce labor costs. This is especially valuable for job shops dealing with production volumes where manual part loading and unloading time can become a substantial portion of the total manufacturing time waiting for employees who may be running other jobs.
- Reduced material waste. EDM’s precision, accuracy, and automation lead to minimal material waste. The ability to cut intricate shapes with minimal kerf widths ensures efficient material utilization, ultimately reducing material costs.
- Enhanced consistency. Automation eliminates the variability introduced by manual operation. This consistency in machining leads to improved part quality, reduced scrap rates, and eliminating reworks, enhancing customer satisfaction and increasing productivity.
- Lights-out operation. Since EDM’s cutting pace is slower than other CNC machining methods, it is ideal for unmanned machining (“lights-out”) production. Job shops can leverage off-peak hours, weekends, and holidays to maximize machine uptime without additional workforce, amplifying production capacity.
- Reduced energy consumption. While EDM machines are known for their cutting precision, they also consume energy efficiently, including when operating in unattended mode. Lower energy bills during non-peak hours contribute to overall operational cost savings, coupled with the EDM tool’s built-in power-saving features.
- Optimized cutting strategies. Automating EDM machinery often requires intelligent software that optimizes the machine’s toolpaths and cutting strategies. This saves time, and can also minimize operator interventions during the production cycle.
- Lower maintenance costs. Many modern EDM machines equipped for automation feature predictive maintenance capabilities. These systems monitor machine and consumables’ health and alert operators to impending issues, allowing for proactive maintenance and reducing unplanned downtime and repair costs.
- Diverse material cutting capabilities. EDM equipment can effectively machine a wide range of materials, including those that are difficult or nearly impossible to machine with conventional milling or cutting methods. Automating EDM manufacturing equipment helps machine shops cut and shape these materials efficiently, opening potential opportunities to accept more jobs and support new machining applications.
The Importance of Advanced CAM and Simulation
Unattended EDM production changes the game for job shops and manufacturers, but its full potential is unlocked when combined with advanced Computer-Aided Manufacturing (CAM) techniques and comprehensive simulation.
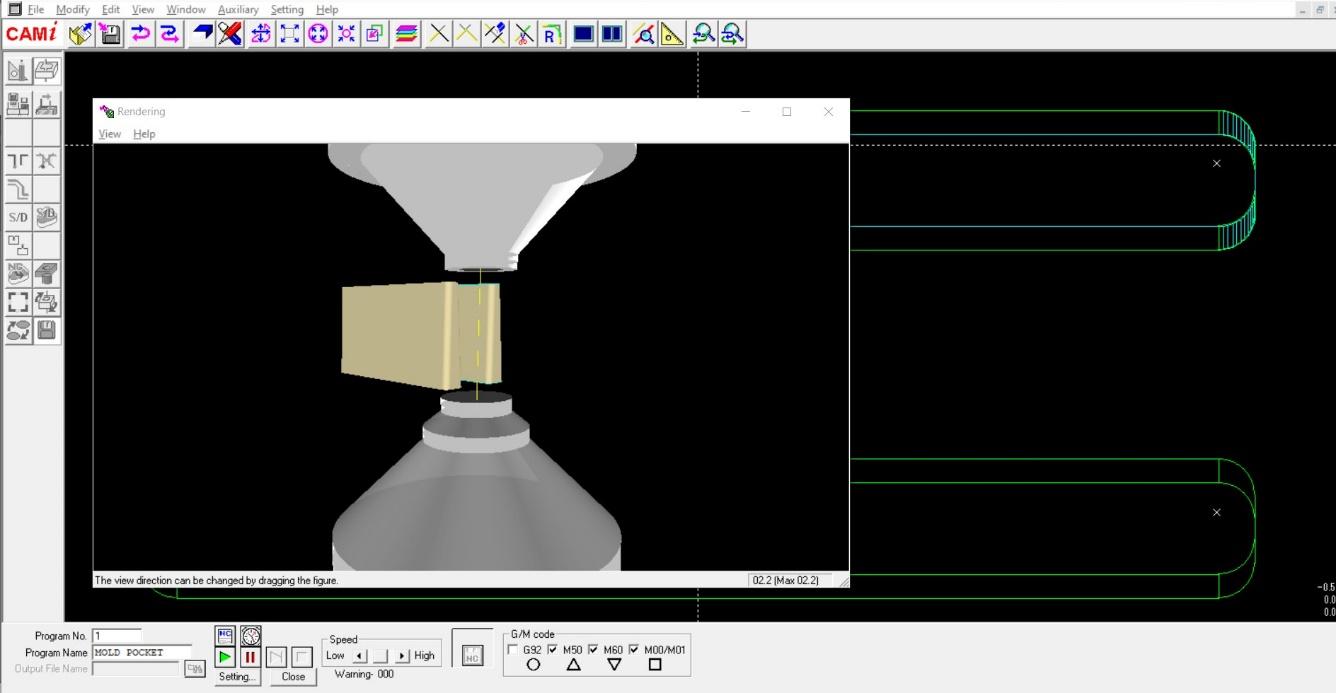
Computer-aided manufacturing (CAM) techniques and comprehensive simulation allow engineers to streamline part design and machining processes.
Streamlining Part Design and Machining
Advanced CAM software goes beyond basic programming, allowing engineers to streamline wire path and machining processes.
With intuitive interfaces and powerful design tools, CAM systems enable the creation of intricate and complex part geometries. This benefits job shops handling high-mix, low-volume production with efficient programming for diverse components.
Optimizing Tool Paths
The technologies that allow the wire EDM to cut precisely can be placed into part programs to ensure that the correct settings have been put in place to cut the geometries correctly and to ensure that operators do not change these settings during production. Coupled with automation, these settings can be changed on the fly as programs for various parts are loaded into the control.
Reducing Setup Time through Virtual Simulations
One of the most significant challenges in machining is minimizing cycle time. Advanced CAM systems integrate virtual simulations that allow operators to visualize the entire machining process before execution. Visualization enables fine-tuning setups, wire paths, tooling, and machining parameters without wasting valuable production time. In addition, it helps detect potential collisions, errors, and inefficiencies in the virtual environment before causing disruptions on the shop floor.
Enhancing Operator Skills
Simulation benefits the machining process and is a valuable training tool for programmers and allows operators the opportunity to train and advance in their careers. This helps maintain a skilled workforce and reduces the learning curve associated with complex machining tasks giving a view to how the machine will operate in advance of cutting a part.
Key Components for Successful Wire EDM Automation
Options for wire EDM automation have evolved significantly as various components and systems have been introduced that enhance precision, efficiency, and unattended operation. Here’s a closer look at possibilities that include wire management, intelligent control systems, and the new frontier of Industry 4.0 and AI-enabled technologies.
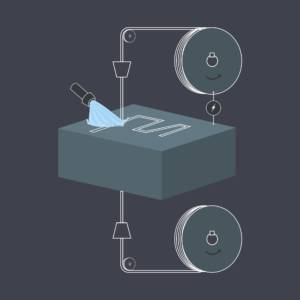
Wire electrical discharge machining cuts metals using a continuously feeding wire electrode.
- Intelligent EDM Control Systems: Intelligent control systems are the brains behind wire EDM automation. These systems utilize real-time spark management to optimize machining parameters, adapt to changing conditions, and ensure consistent, high-quality results by providing real-time monitoring and feedback for process optimization.
- Wire Threading: Automatic Wire threading and repair (AWF/AWR) is the most crucial function for supporting automation because this feature facilitates the initial threading of the wire through the workpiece and subsequent repair. Advanced threaders use servo motors and sensors to ensure reliable and uninterrupted wire threading.
- Intelligent EDM Control Systems: Intelligent control systems are the brains behind wire EDM automation. These systems utilize real-time spark management to optimize machining parameters, adapt to changing conditions, and ensure consistent, high-quality results by providing real-time monitoring and feedback for process optimization.
- Tension Control: Wire tension control systems maintain optimal tension throughout the EDM process. Proper tension prevents or reduces wire breakage and ensures stable machining conditions, especially during long, unattended runs.
- Wire Management and Break Detection: Automation systems for EDM include features that manage wire usage efficiently. These systems monitor wire usage and detect potential wire stress in real time, preventing costly machining errors by adjusting technology to prevent wire breakage.
- Probing Systems: Automated or fully programmable touch probes are frequently used for alignment, part verification, and rotational purposes. This system can enhance the pre-loading of parts and verify the correctness of material once placed in the wire EDM and correct for operator misleading.
- Slug or Core Drop Management Process: To maintain an unobstructed machining process, slug or core drop management is an important factor for machining when cores are to be cut. Having a system in place to prevent the falling of slugs will help keep the automation running and prevent added maintenance. Automated warnings alert operators or trigger corrective actions to prevent disruptions.
- Maintenance: No system is complete without an easy maintenance program. This can be incorporated into the automation based on the product being manufactured.
Get EDM Solutions Customized for Your Shop
Contact Methods to discuss any of the above EDM equipment and automation solutions, or tell our experts what you need from a custom engineered wire EDM application.
Speak to a Methods Expert
Frequently Asked Questions